Seis tecnologías que allanan el futuro de la calibración eficiente
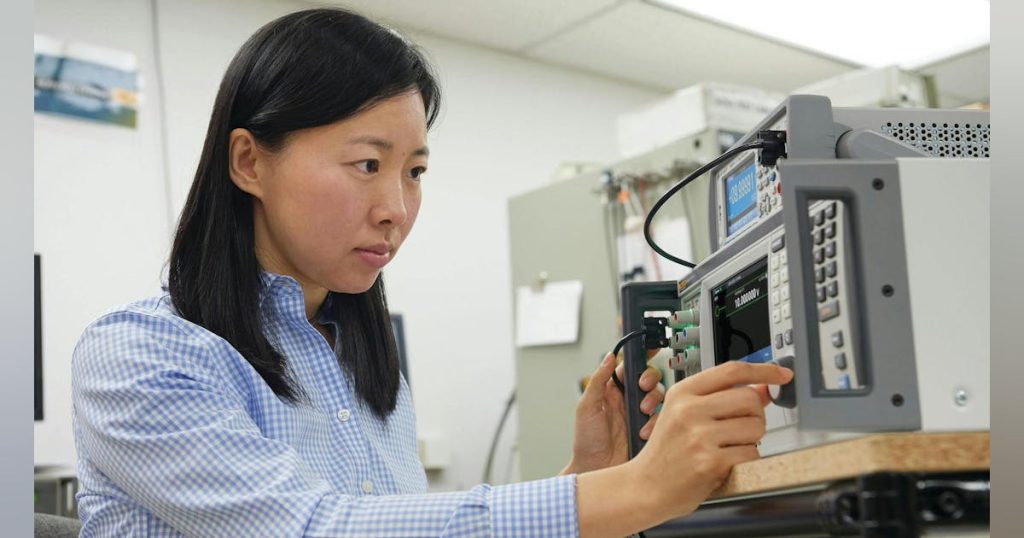
[ad_1]
Aquí examinamos seis tecnologías emergentes que están allanando el camino hacia una industria de calibración más eficiente, precisa y preparada para el futuro.
1. Software automatizado para mejorar la precisión y eficiencia del proceso
El software de automatización de calibración puede transformar procesos y procedimientos manuales en tareas de bajo contacto o incluso sin contacto. Esto reduce el tiempo de calibración porque la automatización acelera las tareas que llevarían mucho tiempo si se hicieran manualmente.
Además, la automatización libera a los técnicos de las tareas manuales y les permite centrarse en tareas más estratégicas y complejas que requieren sus habilidades y experiencia. La integración de este software en su laboratorio de calibración puede generar un aumento significativo en el rendimiento de la calibración y aumentar la eficiencia hasta en un 200 %.
La automatización de las tareas de calibración garantiza una ejecución consistente en todo momento, independientemente de la ubicación o el operador. Esto conduce a una mejor repetibilidad. Además, los técnicos menos experimentados pueden ser guiados a través de los procedimientos, lo que permite a los expertos en la materia dedicar su tiempo donde sea necesario sin correr el riesgo de perder calidad.
2. Inteligencia artificial para aprendizaje profundo y calibración inteligente
No se puede negar que estamos en una nueva era de la tecnología de inteligencia artificial (IA). Cada día se identifican nuevas aplicaciones de estas herramientas y la calibración es uno de los muchos sectores que se benefician de este auge tecnológico.
Los sistemas de calibración impulsados por IA ajustan y optimizan dinámicamente los procesos utilizando aprendizaje automático y algoritmos avanzados. Estos sistemas examinan grandes conjuntos de datos y consideran variables como el comportamiento de los instrumentos y las condiciones ambientales para identificar patrones y tendencias. Esto puede respaldar procesos como la optimización del intervalo de calibración para mejorar la confiabilidad y reducir los costos de mantenimiento.
La industria automotriz ya está tomando medidas para utilizar la IA en el diseño y el desarrollo. A medida que los fabricantes encuentran soluciones innovadoras a los desafíos, como intentar acelerar el proceso de calibración de la unidad de control electrónico (ECU) para vehículos híbridos y eléctricos, la IA impulsa cada vez más este proceso.
3. Los sistemas de gestión basados en la nube establecen el cumplimiento a través de la accesibilidad
El cumplimiento es demasiado importante como para depender de técnicas obsoletas. Si hay algo que puede motivar a las empresas a ir más allá de las bases de datos digitalizadas y las hojas de cálculo estáticas, es un sistema de gestión basado en la nube, y con razón.
Los sistemas basados en la nube almacenan todos sus datos y documentación en una plataforma central. Son accesibles desde prácticamente cualquier lugar y en múltiples dispositivos. Esto hace que sea fácil y rápido obtener la documentación necesaria en tiempo real durante una auditoría para demostrar el cumplimiento.
Además, estos sistemas mejoran los procesos de calibración al brindar visibilidad en tiempo real del estado del instrumento, los programas de calibración y los datos históricos. El acceso constante a los datos permite un monitoreo eficiente y apoya a los técnicos en las decisiones de mantenimiento.
El uso de la nube también ofrece oportunidades para otras aplicaciones de inteligencia artificial y herramientas de aprendizaje automático. El acceso basado en la nube permite a estos programas aprovechar grandes cantidades de datos que pueden anonimizarse y analizarse para aprender más que nunca sobre los dispositivos de medición.
4. Un paso más hacia la Industria 4.0 con certificados de calibración digitales
La introducción del Certificado de Calibración Digital (DCC) pronto podría hacer obsoletos los certificados de calibración tradicionales.
Un DCC no es simplemente una copia escaneada de un certificado tradicional en papel, como un archivo PDF. Más bien, toda la información de calibración se proporciona en un formato de lenguaje de marcado extensible (XML) que es legible por máquina. Esto permite que la información contenida en un DCC se transfiera inmediatamente a procesos respaldados digitalmente. Se utilizan firmas criptográficas para verificar la autenticidad de estos certificados.
La legibilidad mecánica de un DCC es especialmente ventajosa para los procesos de producción y control de calidad. Al eliminar la necesidad de crear y consolidar datos manualmente, se reducen los errores en la transferencia de datos y los cálculos. Además, la automatización habilitada por los DCC agiliza el proceso de producción y garantiza que todas las piezas cumplan con las especificaciones establecidas en los DCC. En general, esta innovación ofrece un gran potencial para mejorar la calidad y confiabilidad del producto.
5. La nueva tecnología de sensores de temperatura reduce a la mitad el tiempo de calibración
Las agencias reguladoras como la FDA exigen que las industrias farmacéutica y de ciencias biológicas calibren periódicamente sus sensores de temperatura. Para seguir cumpliendo, la mayoría de las instalaciones programan la calibración cada seis meses.
Pero a veces los sensores pueden desalinearse entre calibraciones, lo que da como resultado lotes de fermentación arruinados, lo que puede generar enormes pérdidas comerciales. Afortunadamente, las nuevas tecnologías ahora hacen posible que los sensores se calibren solos al final de cada lote, lo que garantiza una precisión continua de las mediciones de temperatura. Este ajuste frecuente reduce significativamente el riesgo de fallos en los lotes de fermentación y las pérdidas financieras asociadas.
La calibración manual de sensores requiere desconectar y volver a conectar el cableado del sistema, lo que requiere mucho tiempo y es propenso a errores. También en este caso, los nuevos avances están contribuyendo a que el proceso sea más eficiente. Un técnico ahora puede girar la parte superior de un sensor para retirarlo en lugar de desconectar los cables, reduciendo el tiempo de calibración a la mitad.
6. Eficiencia y seguimiento mediante calibración remota o calibración sin contacto
La calibración sin contacto es la transmisión remota de datos de referencia estándar desde los laboratorios de calibración a las instalaciones del cliente. El objetivo principal es proporcionar comunicación sincronizada en tiempo real durante el proceso de calibración. Esta innovación recopila parámetros de información del estándar de referencia de calibración y los comparte en tiempo real a través de una red digital dedicada.
Si bien los sistemas de calibración sin contacto aún se encuentran en sus primeras etapas, un estudio de 2022 confirmó su capacidad para calibrar el voltaje de CC. Hoy en día, la calibración sin contacto se utiliza en la industria naviera para controlar el estado de los productos perecederos durante el transporte. A medida que esta tecnología continúa desarrollándose, sus aplicaciones futuras prometen una adopción generalizada en diversas industrias.
La demanda de calibración de precisión está aumentando
El aumento de las inversiones en calibración y la integración de tecnologías avanzadas amplían significativamente las posibilidades. No sorprende que se espere que el mercado global de servicios de calibración experimente una tasa de crecimiento anual compuesta de aproximadamente el 5,6% desde 2024 hasta principios de la década de 2030.
Este crecimiento proyectado resalta la creciente importancia de la calibración precisa en varios sectores, impulsando la demanda de soluciones de vanguardia y contribuyendo a la tendencia al alza del mercado.
[ad_2]
Deja una respuesta